battery junction box automotive View the TI Battery junction box block diagram, product recommendations, . A single gang box, or 1 gang box, is wide enough to enclose only one outlet or switch. Single gang electrical box dimensions vary by manufacturer and type, but are about 2″ wide by 4″ high. Similarly, a double gang box, or 2 gang box, is sized to enclose two wiring devices.
0 · physical location of battery junction
1 · junction box in electrical vehicle
2 · high voltage junction box automotive
3 · high voltage battery junction box
4 · high current battery junction box
5 · battery terminal junction block
6 · battery junction box ford f350
7 · 2022 f350 battery junction box
Spring back occurs when a metal is bent and then tries to return to its original shape. There are two basic views as to why Spring Back occurs, one states that it is due to the displacement of molecules and the other considers Spring Back .
physical location of battery junction
metal fabrication trenton nj
junction box in electrical vehicle
Figure 1 presents a typical BMS architecture containing a battery management unit (BMU), cell supervisor unit (CMU) and a battery junction box (BJB). A BMU typically has a microcontroller .How to design an intelligent battery junction box for advanced EV battery manageme .View the TI Battery junction box block diagram, product recommendations, .
The massive electrification efforts happening in the automotive industry are driving the need to reduce the complexity of BMS by adding electronics in the junction box while enhancing system safety. A pack monitor . Learn how a novel electric vehicle (EV) capacitive-isolation daisy-chain data acquisition IC enables a streamlined junction box time-aligned with battery cell voltage and .The Battery Junction Box is used to monitor and shut down the battery. ☛ With end-of-line test systems we bring safety into the electric vehicle.
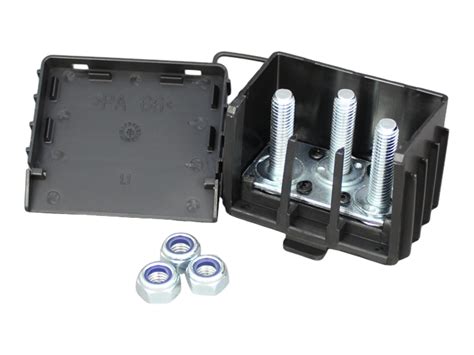
How to design an intelligent battery junction box for advanced EV battery manageme Effective voltage and current synchronization enables precise state-of-health, state-of-charge and . A traditional battery junction box is a relay box or switch box with a power contactor that connects the entire battery pack to a load inverter, motor, or battery charger. Figure 1a shows a traditional BMS.
metal fabrication vaughan
Figure 1 presents a typical BMS architecture containing a battery management unit (BMU), cell supervisor unit (CMU) and a battery junction box (BJB). A BMU typically has a microcontroller (MCU), which manages all of the functions within the battery pack. The massive electrification efforts happening in the automotive industry are driving the need to reduce the complexity of BMS by adding electronics in the junction box while enhancing system safety. A pack monitor can locally measure the voltages before and after the relays and the current through the battery pack. Learn how a novel electric vehicle (EV) capacitive-isolation daisy-chain data acquisition IC enables a streamlined junction box time-aligned with battery cell voltage and temperature measurements.The Battery Junction Box is used to monitor and shut down the battery. ☛ With end-of-line test systems we bring safety into the electric vehicle.

How to design an intelligent battery junction box for advanced EV battery manageme Effective voltage and current synchronization enables precise state-of-health, state-of-charge and electrical impedance spectroscopy calculations that will result in optimal utilization of the EV battery. A traditional battery junction box is a relay box or switch box with a power contactor that connects the entire battery pack to a load inverter, motor, or battery charger. Figure 1a shows a traditional BMS. The High Voltage Battery Junction Box (HVBJB) is located inside the sealed battery pack, and is used to “switch” the high voltage leaving the pack on and off. This internal switch is necessary for safety.
View the TI Battery junction box block diagram, product recommendations, reference designs and start designing.
Learn how a capacitive-isolation daisy-chain data acquisition IC enables a streamlined EV junction box, eliminating multiple components. Electric vehicles (EVs) are powered by huge battery banks (Fig. 1), constructed of long strings of batteries in series that can achieve operating voltages higher than 800 V and an average current of 40 A.
The battery box is intended to manage energy flow between HV Battery and ePowertrain, in addition to manage battery actuators and control charging and discharging operations.
Figure 1 presents a typical BMS architecture containing a battery management unit (BMU), cell supervisor unit (CMU) and a battery junction box (BJB). A BMU typically has a microcontroller (MCU), which manages all of the functions within the battery pack.
The massive electrification efforts happening in the automotive industry are driving the need to reduce the complexity of BMS by adding electronics in the junction box while enhancing system safety. A pack monitor can locally measure the voltages before and after the relays and the current through the battery pack. Learn how a novel electric vehicle (EV) capacitive-isolation daisy-chain data acquisition IC enables a streamlined junction box time-aligned with battery cell voltage and temperature measurements.The Battery Junction Box is used to monitor and shut down the battery. ☛ With end-of-line test systems we bring safety into the electric vehicle.How to design an intelligent battery junction box for advanced EV battery manageme Effective voltage and current synchronization enables precise state-of-health, state-of-charge and electrical impedance spectroscopy calculations that will result in optimal utilization of the EV battery.
A traditional battery junction box is a relay box or switch box with a power contactor that connects the entire battery pack to a load inverter, motor, or battery charger. Figure 1a shows a traditional BMS.
The High Voltage Battery Junction Box (HVBJB) is located inside the sealed battery pack, and is used to “switch” the high voltage leaving the pack on and off. This internal switch is necessary for safety.View the TI Battery junction box block diagram, product recommendations, reference designs and start designing. Learn how a capacitive-isolation daisy-chain data acquisition IC enables a streamlined EV junction box, eliminating multiple components. Electric vehicles (EVs) are powered by huge battery banks (Fig. 1), constructed of long strings of batteries in series that can achieve operating voltages higher than 800 V and an average current of 40 A.

Sheet metal stamping is the process of transforming sheets of metal material into a useful component or part. During the process, metal is fed into a press where a stamping tool, referred to as a die, presses through or into the metal with great force to create the desired shape.
battery junction box automotive|battery terminal junction block